The testing facility: a solution to test robotic technologies with remote drone piloting in Spoke 4
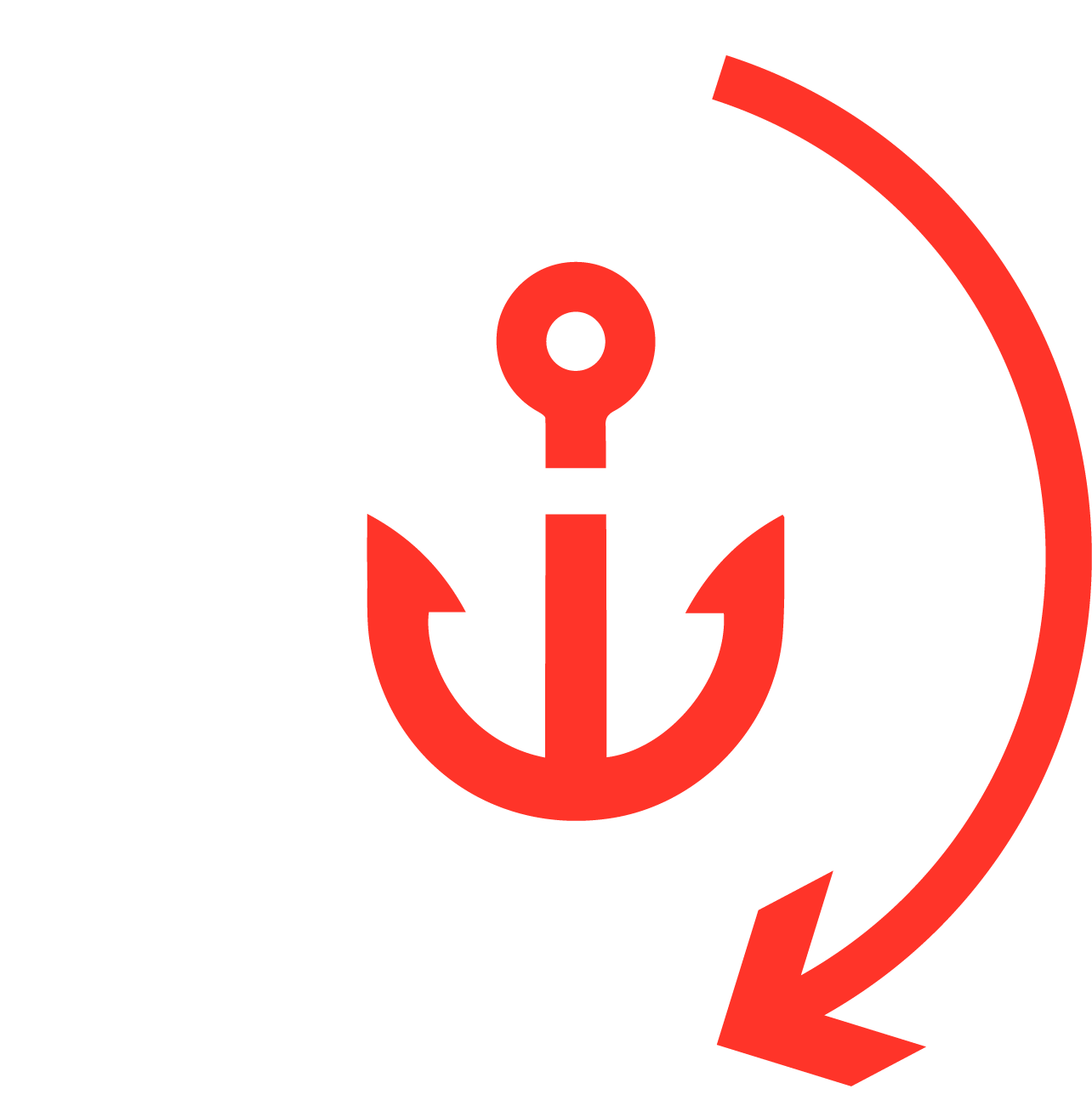
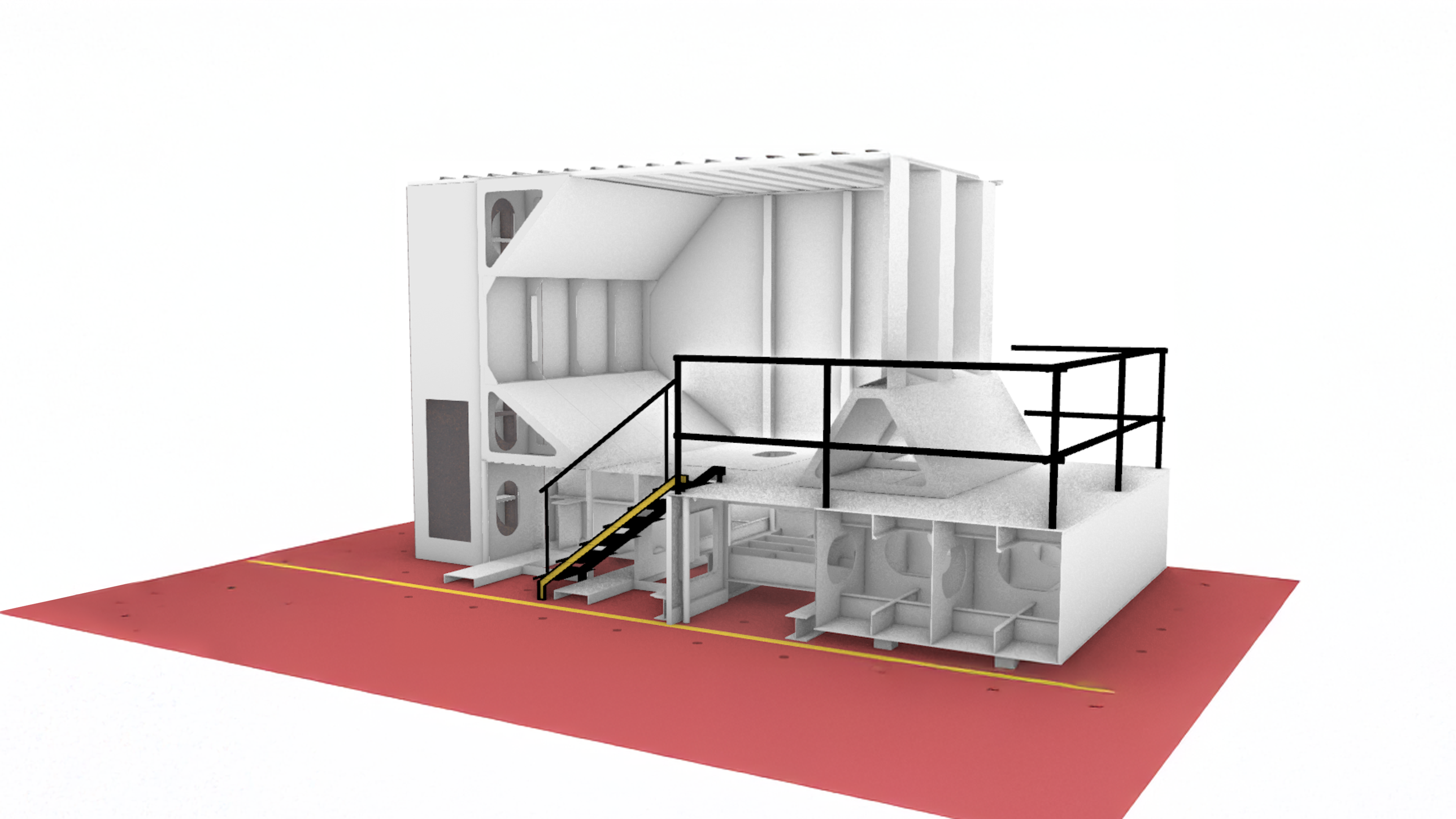
One of the objectives of RAISE’s Spoke 4, on the smart, sustainable and also safer port, is to study and develop new technological solutions for the adoption of digital, robotic and artificial intelligence technologies for the inspection of infrastructures, equipment and ships in ports.
The validation of the effectiveness of the technologies in the automatic detection of potential anomalies will be carried out in a dedicated testing facility, available at the Marine Structures Testing Lab of the University of Genoa. In this test environment, large-scale models of naval structures were reproduced, in different conditions of structural degradation.
The testing facility represents the first test platform in this field, proposed and operational at an international level, patented.
It is a modular construction, consisting of different operating stations, with the possibility of modifying the environmental characteristics in order to simulate the real conditions of an inspection (brightness, humidity, atmospheric agents, pollutants, etc.).
The testing facility is divided into three main sections.
The first (section A) consists of a reproduction of different environments on board a bulk cargo ship (a typical cargo hold, a double bottom, a double side and a ballast tank, with closed and narrow volumes, dark passages, in various conditions of degradation).
The second section (section B) is composed of various equipment specifically designed to test some characteristics of robotic platforms: ability to overcome obstacles, motion on inclined, oily or rusty surfaces, thickness measurement, flight in areas with air currents or water spray, etc.
The third section (section C) is finally formed by a series of ribbed panels that reproduce typical geometries of naval structures and intended for the development of autonomous functions of robots, including the ability to localize the robot itself and the defects detected in an environment with a repetitive structure.
Such a scenario, sufficiently complex, allows to evaluate the localization capabilities in space, the path planning and the possibilities of inspection coverage, both with remote piloting by an operator and with autonomous technologies. It is possible to perform real simulations of an inspection event, proposing a good variety of typical defects, including corrosion in its various forms, damage to the paint, cracks, fractures, distortions and mechanical damage of various kinds.
The human being, with his sensitivity, experience and ability is, to date, in fact, the best subject to make an analysis, used in the practice of naval inspections. Overcoming a tradition consolidated for decades implies, first of all, the ability to demonstrate the validity and effectiveness of a robotic unit or a “digital technology” to support a human inspector.
It is first necessary to establish a common information exchange platform. If the human-machine interaction is now a relatively well-developed topic of study, the relationship between the pilot of a naval inspection robot and a naval inspector is not as in-depth.
The testing facility is therefore an innovative and pragmatic solution to “test” the robotic technologies being experimented in a specific controlled, economic and available test environment, with the aim of promoting extensive and articulated test campaigns.
The next step within RAISE will be, as Cesare Mario Rizzo (UniGe, Spoke 4) pointed out: “To make these inspections remote: the human inspector will be able to receive a data flow directly in his office, remotely”.
Lorenzo Ivaldi (UniGe, Spoke 4) added: “The digital part of the project will mainly focus on the positioning of the cameras for the video flows…The project is based on the management of the drones by an external party, so we will have to define the minimum number of cameras needed, the maximum amount of data that can be conveyed with the remote encrypted connection, the return feedback. In the coming months we will do some tests on the positioning (of the cameras) and on the sizing of the video flows, to optimally evaluate the problems of communication and remote piloting of the drones”.